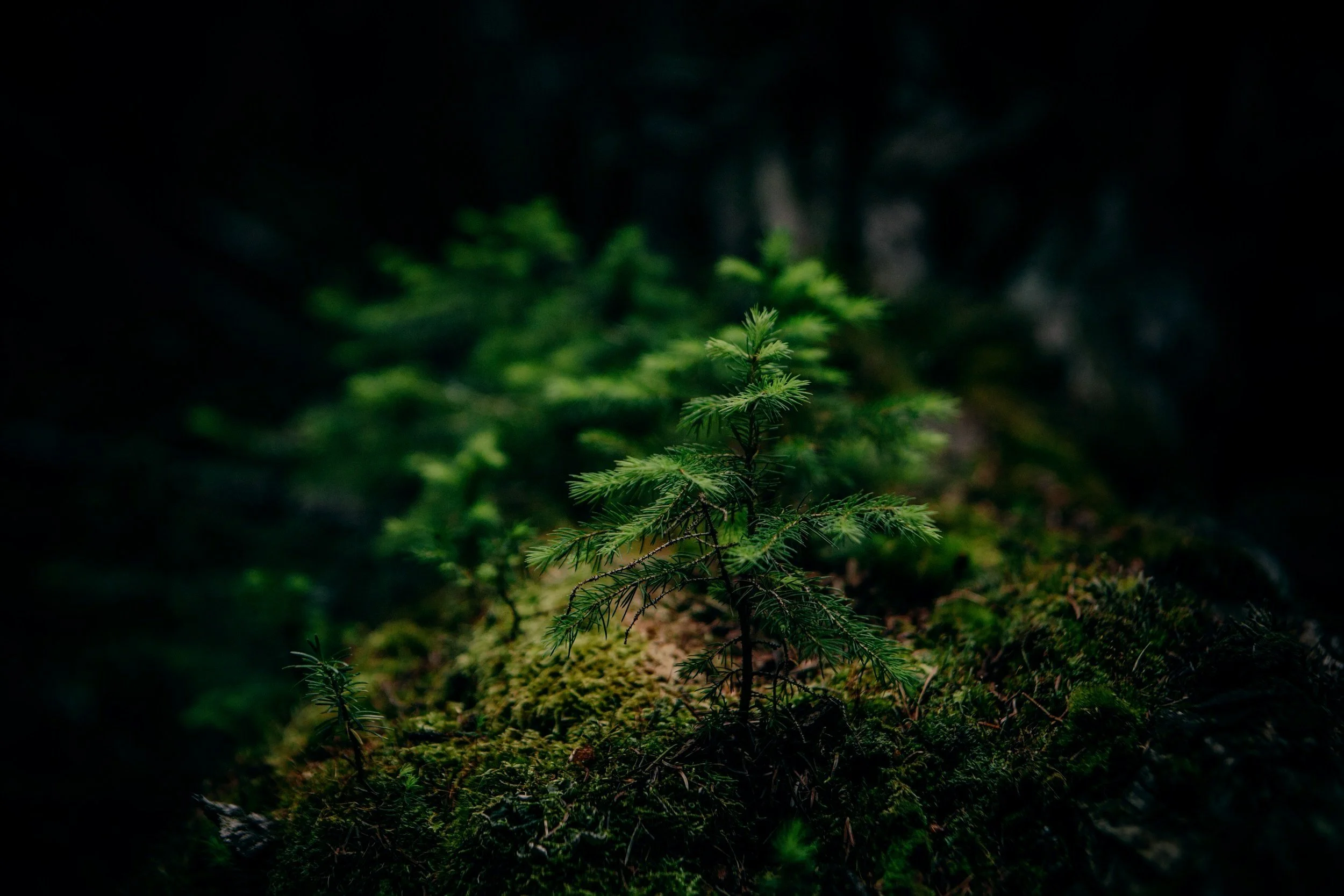
Sustainable innovation meets performance. Harness the renewable strength of lignin for sustainable solutions without compromising quality.
Renol® - A Revolutionary
Bio-based Plastic, Unlocking
the Power of Forest Residues
Sustainable alternative to fossil plastics
At Lignin Industries, we see nature as the foundation for a sustainable future.
Our bio-based plastic, Renol®, is developed from lignin—a natural polymer found in all plants and a byproduct of the forestry and agricultural sectors. While lignin holds great potential, it presents challenges for the plastics industry due to its hygroscopic and low-density powder form, which isn't compatible with the standard granules manufacturers are accustomed to.
We’ve addressed this by combining lignin with a bio-based oil to produce Renol®—a thermoplastic in granule form with high compatibility, making it practical and efficient for industrial use.
A Renewable Source.
Our innovation starts with lignin. Lignin is a natural polymer found in the cell walls of all plants. In trees, lignin constitutes about 20-30% of their structure, serving as a natural and robust binder. It connects cellulose and hemicellulose, contributing to the wood's stiffness and resistance to decay. Following cellulose, lignin is the second-largest renewable source of carbon available.
As a non-toxic & renewable material, lignin presents a valuable opportunity to reduce our reliance on fossil-based resources. Its naturally occurring strength properties enable the development of high-performance, sustainable materials with significantly reduced carbon footprint.
Lignin has the potential to become a much more valuable raw material than being burnt for its energy value. By harnessing this untapped resource, our innovation plays a key role in the circular economy—transforming waste into a renewable solution.
Abundant and Scalable:
A True Bio-Based Solution.
With over 700 million tons of lignin globally each year from both forest and agricultural sources, our innovation is not just sustainable but scalable. This abundant supply ensures the potential for widespread industrial application, making Renol® one of the few truly scalable bio-based materials on the market.
From Nature to Performance:
Introducing Renol®
We convert lignin by combining it with a bio-based oil, producing thermoplastic granules called Renol®. These granules are highly compatible and can be used as a drop-in masterbatch, easily mixed up to 40% with various fossil-based or recycled polymers.
Designed for performance, Renol® helps manufacturers meet sustainability goals without compromising on material strength or quality.
Unlocking Possibilities:
Enabling a Low-Carbon Future.
Our customers, whether they are compounders or converters, use Renol® to create final products or compounds with up to 100% CO2 reduction potential. With Renol®, they can reduce their reliance on fossil-based plastics while delivering products with outstanding performance—driving the shift towards a more sustainable, low-carbon future.

The Ideal Blend: Where Sustainability Meets Performance
Sustainability
Superior Resource
Efficiency
The production of Renol® is a model of resource efficiency.
For every ton of Renol produced, we utilize 0.9 tons of lignin and 0.1 tons of bio-oil—resulting in zero waste.
Secondary
Material
Unlike many bioplastics, Renol® is derived from forest residues—not food-based crops like sugarcane or corn.
This means we aren’t using valuable agricultural land or competing with the global food supply.
CO2
Reduction
Renol® is based on forest residues. Growing trees act as a carbon sink, absorbing more CO2 than they release, which enables significant CO2 reduction.
High
Versatility
Renol® is highly versatile and can be mixed into multiple different plastic applications.
Performance
Drop-in
Solution
Renol® masterbatches can normally be blended directly with existing polymers without compounding.
The use of Renol® masterbatches doesn't normally require any investments from converters and compounders.
Antioxidant
Features
Renol® prevents oxidation/degradation which improves recyclability.
Temperature
Resistant
Renol® has a unique property regarding temperature resistance being able to be processed up to at least 230 degrees without being burnt.
Low Density
Material
Renol® enables lightweight material since the density of Renol is close to 1 kg/dm3.
The low density significantly reduces weight compared to fillers or other biobased materials.
Biobased
Material
Renol® is 100% biobased.
Lignin from the forest or agricultural industries, mixed with a biobased oil.
Recyclable
by Design
Renol® masterbatch enables end-product recyclability.
Renol® remains stable through multiple cycles, proven to enhance PE, PP and ABS properties in recycling.
Reduce your carbon footprint with Renol®
Growing trees act as a carbon sink, absorbing more CO2 than they release, which makes Renol® a carbon-negative material.
Calculated by SWECO, 2024.
According to ISO 14040, ISO 14044 and ISO 14067 and comprimises cradle-to-gate data.
Sustainable materials for various applications
Explore our materials for a specific manufacturing technology or have a look at our industry specific solutions
LDPE Films
Innovative e-commerce bags based on recycled plastics and lignin, for reducing fossil use and lowering CO2 emissions. Produced in close collaboration with our film partners in Europe.
Polypropylene Applications
Through customers we are currently developing applications within electronics, construction, home appliances and automotive for reducing the fossil use of polypropylene and lowering CO2 emissions.
ABS Applications
Through customers we are currently developing applications within electronics, construction, home appliances and automotive for reducing the fossil use of ABS and lowering CO2 emissions.